7 Common Label Issues (and 1 Step to Avoid Them)
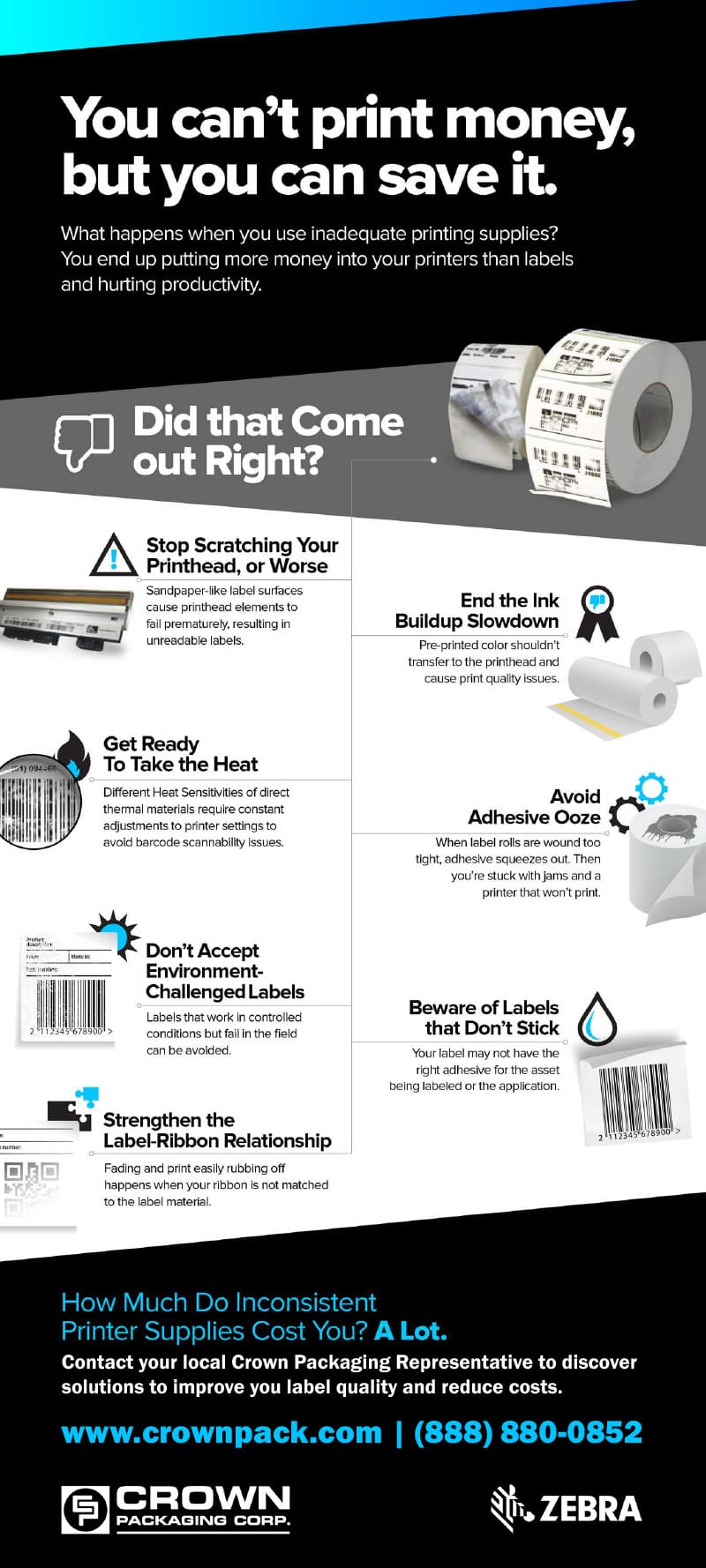
Labeling expenses account for an average of 5-10% of a warehouse’s total operational expenses.
However, under-performing labels contribute to printer downtime, misplaced inventory storage, and slowed operations, ultimately costing more than the initial investment in quality labels.
Consequently, operations must learn to recognize the tell-tale signs of inadequate labels before they cause costlier issues. These signs include:
2. Ink buildup – Label ink must also be stringently tested along with the rest of the label to avoid ink buildup. This can be verified by checking if your printhead is stained with ink from your pre-printed color labels.
3. Leftover adhesive ooze – Similar to the ink buildup, seeping adhesive can also leak out if labels are wound too tightly. This contributes to leftover debris in the printer, resulting in eventual jams and downtime.
4. Peeling edges – Adhesive strength is affected by the environment’s humidity levels and temperatures, so if labels begin to present peeling edges, adhesives may not be suitable for your storage area. To further verify proper adhesive selection, labels should be monitored even after they leave the warehouse to make sure labels survive outside of controlled conditions.
5. Fading barcodes – Thermal and direct thermal printing use heat to create barcodes, which is why heat-sensitive labels may harm inventory identification as barcodes begin to fade under different temperatures.
6. Weak label-ribbon relationships – If labels don’t properly match ribbons, barcodes can be rubbed off as they are moved down the supply chain, ultimately compromising legibility and product identification.
7. Missed compliance codes – Finally, because labels carry important product information, your operations may pay more fines and fees if they completely fall off while moving down the supply chain.
TroubleShooting Labeling Issues
Since there is no one-size-fits-all labeling solution that can truly adapt to your specific application requirements, the first step to targeting these issues is to assess your workflows to optimize your labeling process to best match application and storage environments.
After noting challenges and goals, Crown Packaging’s labeling experts can build an end-to-end solution leveraging best-in-class technologies like Zebra’s Certified Consumables and enterprise-ready printers.
By implementing durable labels that are built with challenging environments in mind, warehouses can protect inventory from misplacements, delays, and spoilage, ultimately protecting the bottom line.
IMprove Labeling Processes with CRown Packaging
Contact Crown to discuss upgrading your labeling and identification workflow with better materials or optimized equipment.